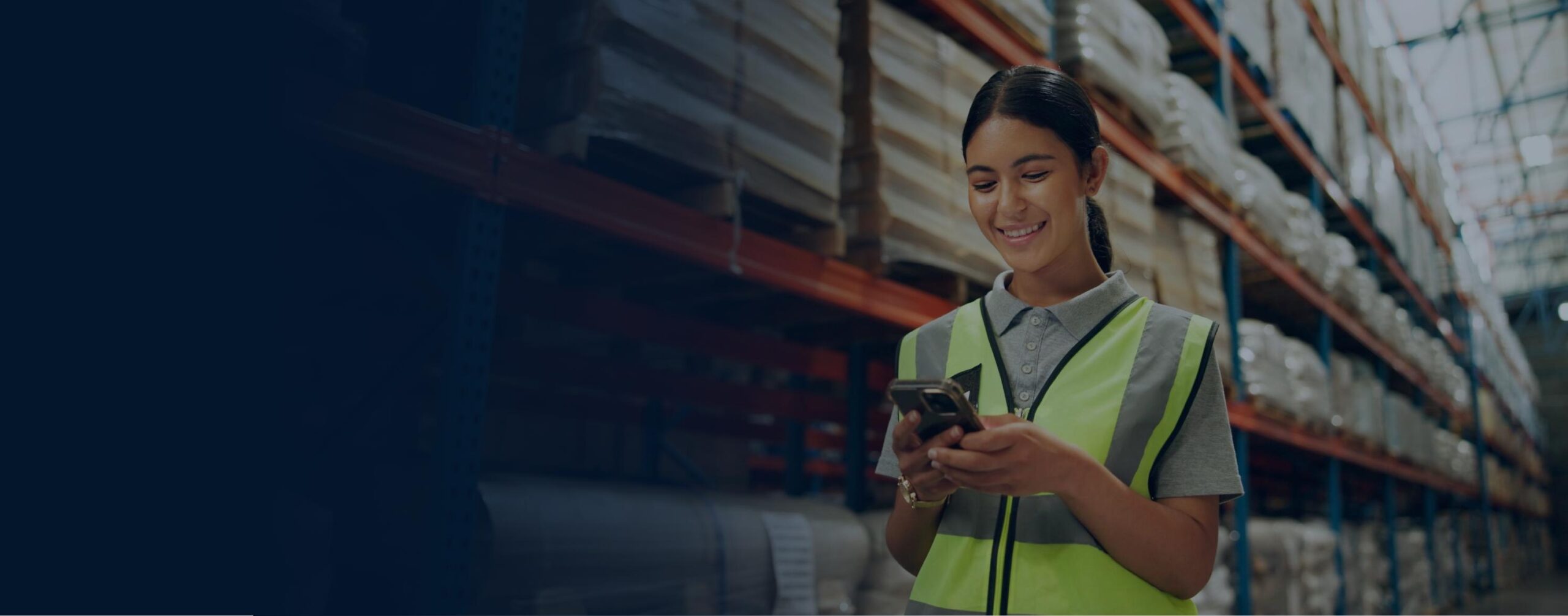
SyteLEAN
Calculate optimum inventory levels based on actual sales and usage, reducing excess inventory and shortages, without the complexity of MRP/APS. The SyteLEAN PullSystem is an easy-to-use inventory management system for items that are regularly purchased or manufactured.
Get Started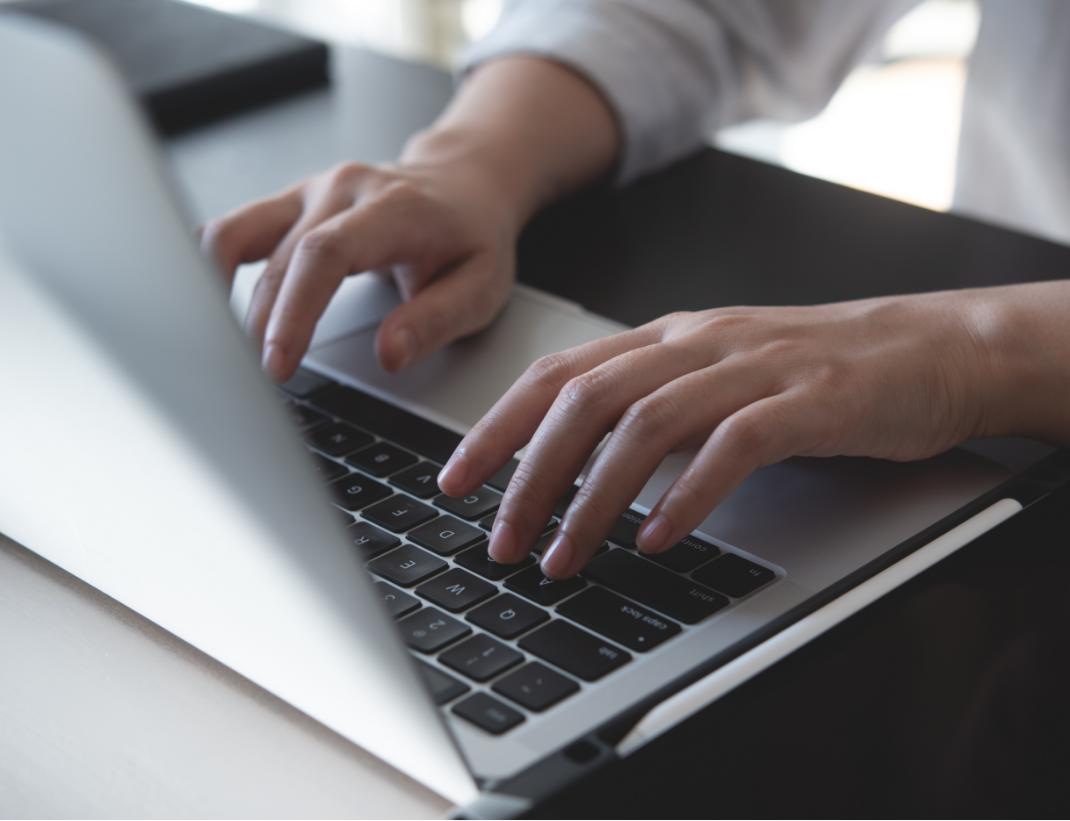
Key Features
Automatically Calculate Safety Stock, Trigger Point and Maximum Supply Quantities for PullSystem items
Define Service Level policies maintain at the optimum level to meet your fluctuating demands
Use the Material Planner’s Workbench or Order Action Report to confirm your Replenishment Orders
APICS standard statistical calculation for Safety Stock
Works in tandem with SyteLine Forecasting with to control weighting of history vs. forecast
Calculate Days of Inventory On- Hand and in the Supply chain for Pull System items
Purchased and manufactured item replenishment based upon a dynamic demand-driven Trigger Point
Visibility into Spike Demands and Supplier Forecasts
Utilities to identify which inventory items are best managed by a Pull System
Compatible with all SyteLine versions