Industry Insights into Food Processing Manufacturers
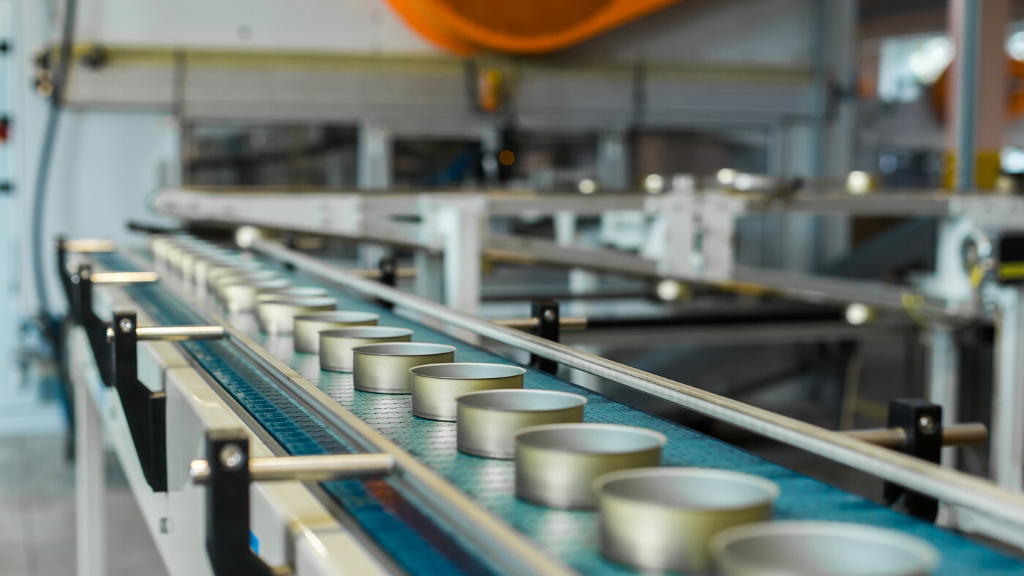
Food process manufacturing is big business. Its revenues add up to nearly $700 billion each year. In fact, the industry is responsible for one out of every six dollars generated by American companies.
But as big as these manufacturers are, it seems as though their challenges are even more significant. Unpredictable consumers, tight federal regulations, and increasing pressure from influential retailers are creating an environment in which food manufacturing companies must be creative and innovative to maintain profits.
Other inherent issues include the shorter lifecycles of food products and the ever-increasing number of SKUs, making it a constant challenge to satisfy traceability requirements. All of the variations in packaging, customization, and seasonal products add to the more pronounced struggle today than it was a few years ago.
Since each new SKU entails new processes, different equipment, and a host of risk factors, the pressures on food process manufacturers continue to grow. With estimates from the CDC that 48 million people (about one in six Americans) will suffer a foodborne illness during the year (and another 128,000 will be hospitalized), it isn’t surprising that the food industry deals with a raft of regulations.
Here are some additional insights into the industry.
Food processors will be adding NFPA 652 to their list of requirements.
Along with several other industries, food processors will be facing the requirements of NFPA 652 in 2020. The standard provides the requirements to prevent dust-related fires, flash fires, and explosion hazards from dust collection and handling equipment.
Preventive measures will include the following:
- Implementing a hazardous dust inspection, testing, housekeeping, and control program
- Using proper dust collection systems
- Regular inspections for dust residues in open and hidden areas
- If ignition sources are present, use cleaning methods that do not generate dust clouds
The food and beverage industry is facing a worker shortage.
Before COVID-19, unemployment was at a 17-year low, adding one more element to the food processing industry’s growing list of challenges: a shortage of workers. According to a 2016 survey sponsored by an international food company, only 12% of adults would consider a career in manufacturing and engineering. Many of today’s job seekers want perks that food manufacturers typically do not provide for instance, remote work and educational benefits.
Since employees are directly responsible for meeting production deadlines, forecasting labor demand accurately is crucial. Inaccurate forecasts will become evident on the bottom line.
Retention is also a challenge.
While the food industry, on the whole, is finding it difficult to attract new workers, the beverage companies, in particular, are having issues hiring and retaining skilled labor for their operations. One of the primary reasons is that employees are not receiving adequate training in these production-intensive environments.
The extremely high production volumes and low margins eliminate the possibility of shutting down a line for a block of training. Also, many of these companies are running 12-hour shifts, resulting in fatigue that eventually leads to burnout.
There is a reason for hope.
Enterprise resource planning (ERP) solutions can help the food processing industries to address its many challenges. Giving workers real-time visibility and transparency over their schedules will help combat burnout and increase your company’s retention rate. Workers can request time off, volunteer for shifts, and swap assignments through the system, which boosts morale and frees the scheduler from dealing with grievances in-person.
Coping with the worker shortage will be easier because your ERP system will provide real-time analytics to determine demand and allow you to control any gaps in the workforce proactively. When you get these real-time updates, you can decide whether to schedule overtime for your current employees or to hire temporary workers.
Finally, providing an unbroken chain of custody over each product shipment is at the core of most food safety regulations. Once again, a record of how products are produced and what went into them should be consistent and traceable from product lifecycle management (PLM) and continuing through procurement, production, quality management, and distribution. Having all this data in one ERP system, and being able to retrieve it quickly, provides complete traceability for regulators and customers alike.
The ERP experts at Decision Resources are on standby to provide the information you need to streamline functions, improve productivity, and introduce and maintain an integrated and more efficient way of doing business within your food and beverage manufacturing environment. If you’re ready to take a step toward transforming your business with an ERP, please get in touch through our online contact form, call 412-562-9660, or email us at info@decision.com.
Similar Blogs
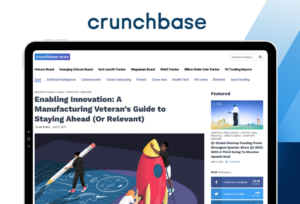
Decision Resources Featured on Crunchbase
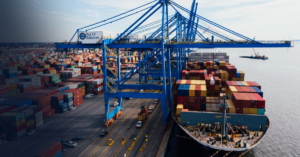
Chips, drugs, and steel — how to prepare for Trump tariffs
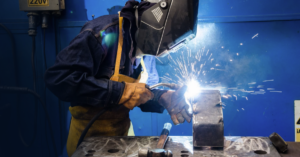