Ensuring Quality Control in Manufacturing in Times of Crisis
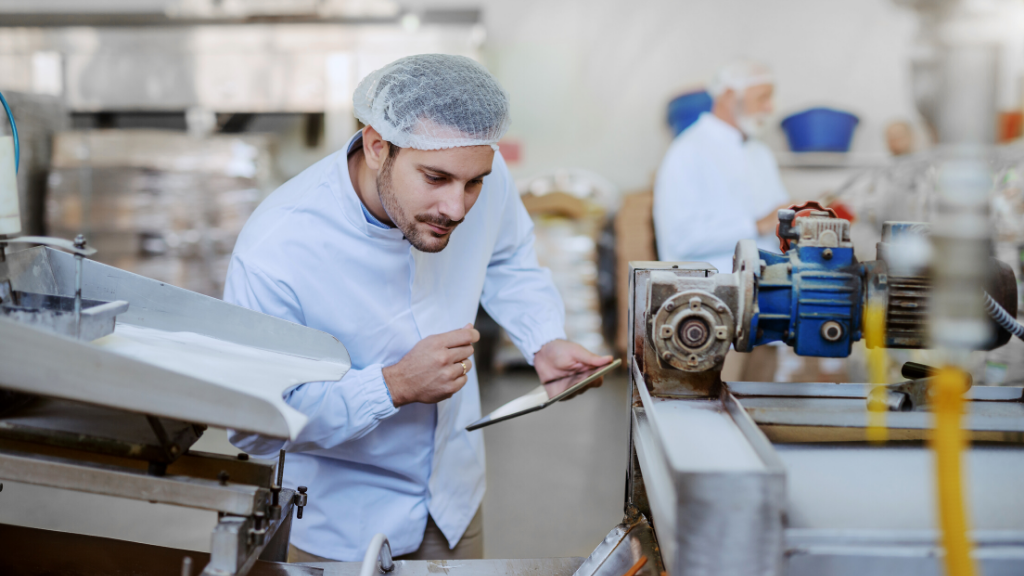
Quality is a concern for all manufacturers, but for food and beverage manufacturers, it’s vital. And in times of crisis, a systematic approach to quality helps to contain costs, improve productivity, manage inventory, and deliver the products that customers expect.
A quality program must incorporate quality control and quality assurance if it’s going to be effective. Quality control pinpoints defects in a finished product before you ship it to the customer. In contrast, quality assurance scrutinizes the entire production process, by ensuring the quality of incoming raw materials or components, following transparent production processes, and testing the product. A successful quality program must administer both control and assurance.
In the absence of quality assurance, it becomes much more challenging to identify where the problem originated. And without the assistance of technology, which comes in the form of enterprise resource planning (ERP) software, monitoring the process is next to impossible.
Here are some quality-related suggestions that are crucial at any time, but even more so during the era of COVID-19.
Always define quality from the customer’s perspective.
Many manufacturers have a goal of improving their product without knowing what purpose the “improved” product will serve. By adding some cost, they believe, their goods will last longer and result in happier customers. But is it a more expensive product that the customer wants, even if it means it will last longer?
A better plan would be to find out what the customer needs. Assign someone in sales or marketing to be your customers’ advocate. You might discover that they have a different definition of “high-quality.” If that’s the case, you can begin meeting those requirements while working on holding down costs.
Take a team-based approach.
Quality doesn’t happen in a vacuum. To make permanent and consequential changes in your manufacturing processes, it will take a team mindset. Involving various departments in the quest for improved quality will yield multiple perspectives. Some of those voices might know the process history, and they can share insights into why the process has evolved into what it is today. Those reasons could prevent you from repeating a former problem. So, by combining numerous perspectives and the process history, you can make meaningful improvements.
Traceability is vital.
The supply chain of any food and beverage manufacturer must be traceable and verifiable. While traceability can allow for a quicker response and save lives, it’s always preferable to catch any issues early on. Transparency at every juncture in the supply chain is now the standard in food and beverage manufacturing, and every organization must be ready to implement it.
The issue of traceability takes on added importance when you consider the advent of global supply chains. An integrated platform, such as a cloud-based ERP solution, will keep all of your data in one location where anyone who needs it can access it. You can also keep track of quality control key performance indicators (KPIs) and trace any failed batches back to their source.
Automate your processes.
Generally speaking, if you can eliminate more human input from your operation, you will have fewer errors. Automating your manufacturing process comes with several benefits for food and beverage quality control. They include:
- Transparency
- Worker safety
- Improved efficiency
- Lower costs
Technology is incredibly valuable to today’s food and beverage manufacturers. These ERPs can catch quality-control issues at the source. So when you are evaluating the costs and benefits of adding an ERP to your enterprise, keep in mind the quality-control advantages these systems will provide.
Communicate the cost of quality to the entire organization.
Fixing defects at the source of the problem is much less expensive than catching it right before it’s shipped or, worse yet, after it leaves the plant. Everyone on your staff should be trained to understand the costs associated with replacements and a tarnished reputation.
Emphasize the cost of quality across the organization, including internal issues such as waste and reworks, along with any external failures like recalls, refunds, and possible lawsuits.
Evaluating, upgrading, or choosing your ERP system for quality control and compliance requires expert insights, especially now. The entire team at Decision Resources has the expertise and experience to ensure your ERP has what it takes to fulfill your company needs and customer expectations during this time. Please get in touch through our online contact form, call 412-562-9660, or email us at info@decision.com.
Similar Blogs
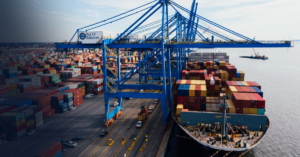
Chips, drugs, and steel — how to prepare for Trump tariffs
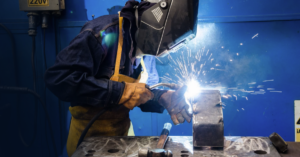
How Steel Manufacturers Forge Ahead with Infor CloudSuite Industrial ERP
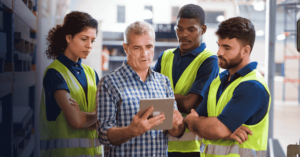