3 Questions Food Manufacturers Ask About ERPs
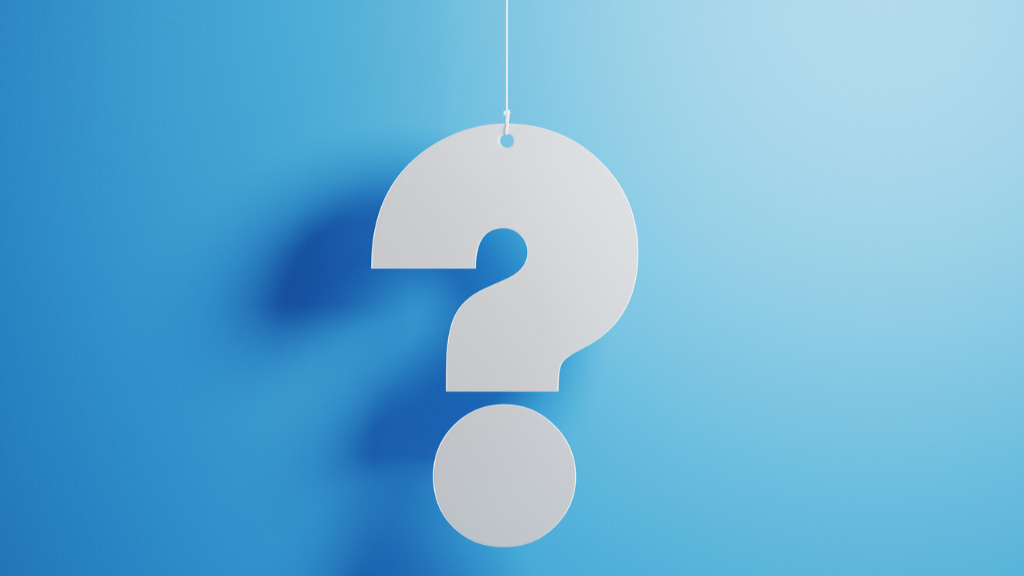
There are many considerations for food manufacturers when it comes to enterprise resource planning. Food manufacturing is complex and highly regulated. This industry requires constant and strict adherence to compliance, ongoing assurance of food safety and sanitization protocols, and continual responsiveness to customer demand, all while managing steep competition, supply chains, pricing shifts, and changing market conditions. Productivity, efficiency, and operational optimization are top-of-mind.
Moving away from siloed functions and into a fully integrated ERP software can provide food and beverage manufacturers with actionable insights that can transform their manufacturing environment across the areas of finance, purchasing, sales, production, inventory, quality, compliance, and more.
Here are our top 3 questions that food manufacturers commonly ask about ERPs to identify how ERP can innovate and improve their food and beverage manufacturing operations.
1. What are the benefits of using ERP software? ERP has nearly unlimited benefits, especially for food and beverage manufacturers. First and foremost, ERP systems offer information across every facet of your manufacturing enterprise, all updated and accessible in real-time, and when cloud-based, from anywhere on any device. From there, your entire organization can connect, utilize, share, and apply data across departments, users, and internal and external stakeholders, such as third-party vendors or consumers.
Key benefits of ERP software include:
- Faster deliveries of products
- Improved communication with employees, departments, vendors, and customers
- Enhanced supply chain visibility and inventory control
- Increased productivity
- Improved shipping operations
- Reliable tracking of leads, quotes, and new opportunities
- Improved supplier relationships
- Automation of formerly manual processes
2. How will ERP meet company needs? Food and beverage manufacturers know that this industry moves quickly. Innovation and responsiveness are essential. When working with an ERP partner, your ERP consultant will evaluate and assess your current manufacturing environment to ensure that your chosen ERP systems address current company needs, integrate with existing systems, and position for future growth. ERP is highly flexible, scalable, and customizable. Food manufacturers can work with their ERP consultants to adjust and scale ERP features and modules for seasonality, growth, market changes, and other considerations.
3. How can ERP improve customer relationships and customer service expectations? You know that your customers sustain your business. With ERP solutions, your company can provide superior customer service across many areas to ensure you’re building long-lasting, enterprise-sustaining customer relationships. Your ERP systems will collect and organize customer purchase histories, offer a complete view of each unique customer, prioritize high-value customers, and give your customer-facing departments the support, data, and information they need to address issues and transform relationships.
An enterprise resource planning (ERP) software solution is a significant step towards achieving operational excellence, improving productivity and performance, delivering on customer expectations, and more.
At Decision Resources we have been helping food and beverage manufacturers, and manufacturers across industries, get the most from their business systems and technology for more than 40 years. Leverage our ERP expertise to help you gain valuable insights into your supply chain, boost your operational efforts, and manage your production effectively and efficiently. Contact us anytime.
Similar Blogs
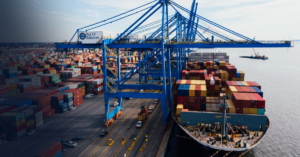
Chips, drugs, and steel — how to prepare for Trump tariffs
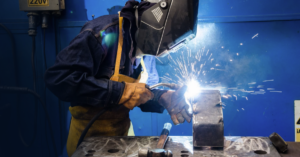
How Steel Manufacturers Forge Ahead with Infor CloudSuite Industrial ERP
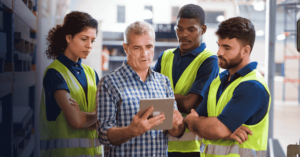